
La importancia de filtración de aceite en riñón o diálisis
Por Richard Widman
Vivimos y operamos maquinaria en ambientes llenos de polvo, hollín, humedad, humo, y otros contaminantes. Tradicionalmente miramos análisis de aceite, vemos contaminantes, y paramos los equipos para cambiar aceite o continuamos con ojos cerrados porque no tenemos el presupuesto para comprar los litros, turriles, o lo que sea para hacer el cambio, o postergamos el cambio porque no se puede parar la máquina, esperando que tal vez no sea muy serio el daño que hará ese contaminante. ¿Pero serán que son las mejores decisiones?
Este es el Boletín #196 de nuestro programa de Boletines Informativos mensuales. Todos los boletines están disponibles en formato pdf en https://www.widman.biz
Varios estudios y estimaciones hechas por universidades e instituciones de renombre concluyen que 70 a 85 porciento de las fallas de maquinarias, son causados por el uso de un lubricante inadecuado o contaminado y pocas veces es estudiado tanto a nivel químico como a nivel físico.
Contaminación es:
- Polvo y agua (de forma directa o a través de aire húmedo) que entran por los respiraderos, retenes, tapas sueltas, etc.
- Aceite diferente rellenado por equivocación.
- Tierra en baldes, embudos, bidones, etc. utilizados para rellenar.
- Tierra en los picos de bombas.
- Tierra y humedad que entra a los tambores en uso cuando dispensen aceite, o al calentar y enfriar el fluido.
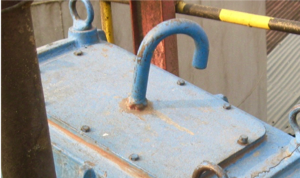
Al calentar y enfriar, el aire de la planta es mezclado con el aire del equipo, pasando después al aceite.
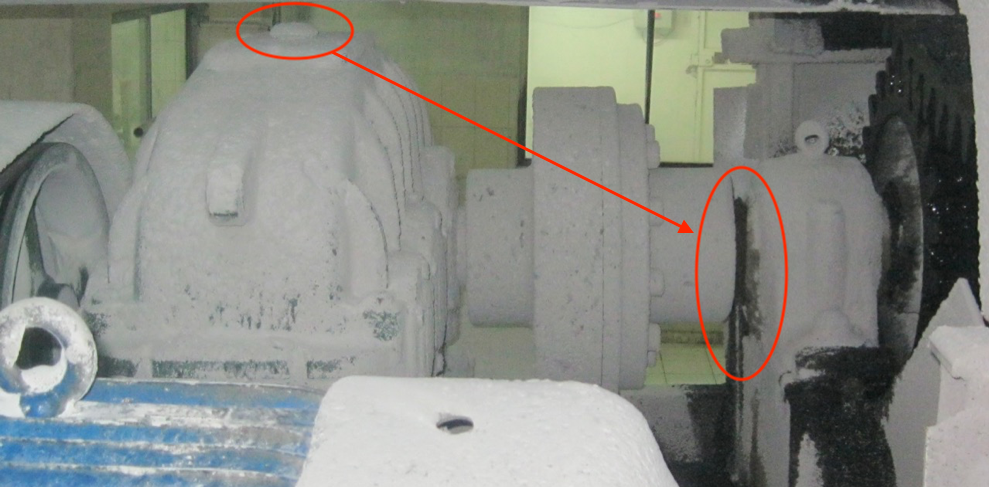
Para determinar el grado de contaminación que tiene el fluido en nuestro equipo, debemos tomar una muestra del aceite mientras el equipo esté funcionando. Esto debe ser tomado con mucho cuidado si queremos tener resultados confiables. Es decir, la toma de muestras debe ser de acuerdo con un procedimiento y plan de muestreo. Enviamos la muestra al laboratorio para un análisis con conteo de partículas.
El reporte del laboratorio nos dará una visión de la condición del aceite comparado con las normas o promedios. Debemos tener personal en la empresa (o tercerizado) para comparar estos resultados con nuestros objetivos y ayudarnos a tener una visión de la efectividad de nuestro plan de mantenimiento. Nos indicará el camino a seguir con el aceite o la máquina, teniendo en cuenta los contaminantes y la degradación.
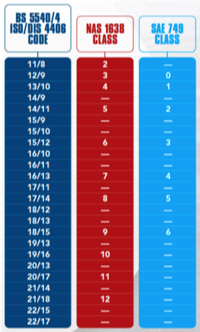
Hay pequeñas diferencias en la medición, pero en general se puede cruzar las tablas como mostramos aquí.
En aceites muy viscosos, a veces no se muestra las partículas debajo de 6 𝜇m.
Normalmente incluimos los tres niveles.
- Sobre 4 𝜇m
- Sobre 6 𝜇m
- Sobre 14 𝜇m
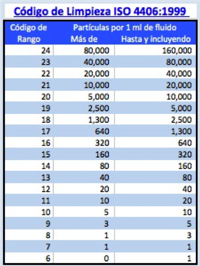
Para simplificar la explicación del nivel de limpieza, se abrevia o convierte el nivel actual a un numero más fácil, representativo, para anotar, graficar, etc.
Si hay entre 80,000 y 160,000 partículas, en 1 ml de fluido, sobre 4 𝜇m, por ml, se clasifica como 24/xx/xx.
Y si 30,000 de estos son sobre 6 𝜇m, se clasifica 24/22/xx.
Y si 8,000 de estas partículas son sobre 14 𝜇m, terminamos con 24/22/20.
Tocamos esto en detalle con medidas de partículas en el boletín 129.
Podemos implementar sistemas de control, entrenamiento, seguimiento, etc., pero la realidad es que, en general, nuestro aceite está “sucio”. Tenemos dos métodos de ver la contaminación:
- Conteo automático, en línea o en laboratorio, en detalle, aunque burbujas pueden ser leídos como partículas.
- “Patch test” donde miramos las partículas en una membrana a través de un microscopio.
Vemos que pasaron los primeros 18 meses analizando su aceite sin tomar acciones efectivas. Bajaron la contaminación por partículas de 34 mil a 27 mil (sobre 4 𝜇m) en cada ml, y después a 23 mil. Todas las muestras están dentro de la clasificación 22.
Después de la tercera muestra, a los 18 meses, tomaron acciones o cambiaron aceite, y bajaron la contaminación de 23 mil a menos de 5 mil, mejorando la vida útil del equipo.
La próxima muestra indica otra mejora, bajando la contaminación total a 1300 partículas y llegando al objetivo para ese equipo. Pero la última muestra, a la extrema izquierda, muestra una subida a 4000 partículas, o sea una contaminación por algún lado.
Ejemplo 1:

En el próximo ejemplo, tenemos el mismo periodo, con problemas más severos, que nunca fueron solucionado completamente.
Empezaron con casi 107,000 partículas sobre 4 𝜇m por ml, mejorando a 73,000 𝜇m, por ml, mejorando a 73,000 𝜇m, y después manteniendo entre eso y 88,000 partículas en los siguientes cinco semestres.
Ejemplo 2:

¿Cuál es la solución?
Tradicionalmente, drenamos lo que sale del aceite viejo, tal vez limpiamos el reservorio (cuidado con lo que llamamos “limpieza” del reservorio), y cargamos el aceite nuevo por baldes, bidones, etc. A veces, se saca una bomba de un tambor para colocar en otro, mezclando los aceites.
Asumimos que el aceite nuevo es limpio, y no consideramos la contaminación por el método de transportar y cargar el aceite.
Pero, ¿Cómo es el aceite nuevo? Aquí colocamos el conteo de partículas de 15 tambores de aceite nuevo, de tambores idénticos en el almacén, sin haber sido abiertos; éstos a veces llamados New Oil, Aceite nuevo o Aceite Virgen. Mientras el aceite de 13 tambores estaba relativamente limpio, el de dos tambores no era apto para ninguna máquina.
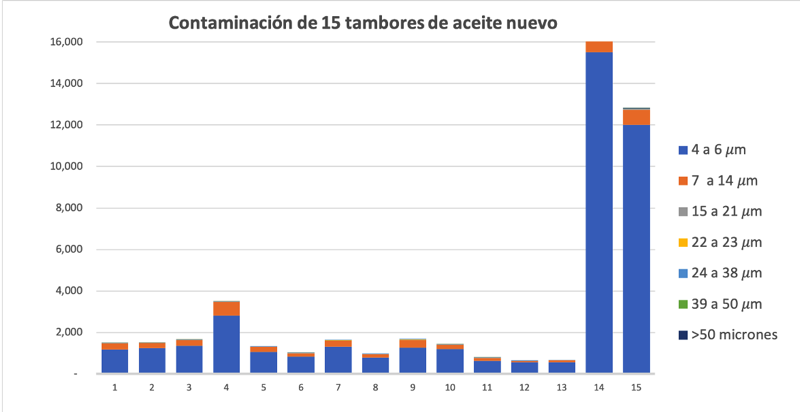
Turril 12
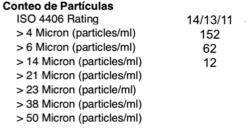
Turril 14
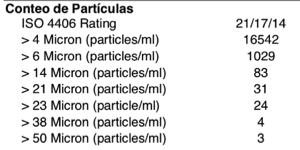
El turril 14 es el más sucio de todos, y no debería entrar en ningún sistema. Ni es apto para reductores de baja carga. Además del total de partículas sobre 16,000 por ml, cada ml tiene 3 partículas visibles (>50 𝜇m).
Efectivamente todos estos aceites son más limpios que los del ejemplo 2 que vimos arriba, pero no son bastantes limpios para cuidar el equipo.
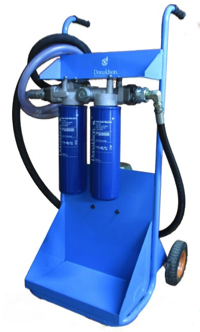
Es por estas razones que el aceite debería ser filtrado con un filtro bien fino al cargarlo al sistema. Y después de cargar el sistema, el aceite debería ser filtrado en uso, eliminando todas las partículas que quedaron pegadas en diferentes compartimientos, mangueras, y válvulas.
Un equipo como este, con filtros, por ejemplo, Donaldson de código P568666 de 4 𝜇m en cada ml.
El aceite fue sacado del equipo, limpiaron el reservorio, y filtraron el aceite al cargarlo. El aceite filtrado que entró al reservorio tenía solo 152 partículas sobre 4 𝜇m por ml. Una reducción de 99.91%
- El dializador debe tomar el aceite del fondo del tanque o de la válvula de descarga, y devolverlo a la parte superior del mismo tanque, filtrando el volumen de aceite por lo menos 7 veces.
- Ejemplo:
- Sistema de 1000 litros.
- Bomba de 30 litros por minuto.
- 1000 x 7 = filtrar 7000 litros
- 7000/30 = 233 minutos = 4 horas (+/-)
Miramos un ejemplo real, donde el tanque lleva 5000 litros de aceite hidráulico. Antes de filtrarlo, el aceite tenía más de 171 mil partículas sobre 4 𝜇m en cada ml.
El aceite fue sacado del equipo, limpiaron el reservorio, y filtraron el aceite al cargarlo. El aceite filtrado que entró al reservorio tenía solo 152 partículas sobre 4 𝜇m 𝜇m por ml. Una reducción de 99.91%
Antes de filtrar
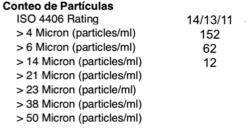
Después de filtrar
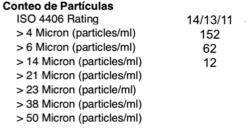
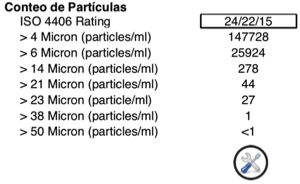
El conteo de partículas muestra que la mezcla de aceite súper-limpio y los residuos en el equipo termina con una limpieza de 24/22/15. Ahora quedó con un poco menos de 148 mil partículas sobre 4 𝜇m en cada ml.
No sabemos las condiciones de limpieza de la máquina, tampoco de los conductos y cuando ingresa el aceite gira como remolino, levantando partículas que dejó el anterior aceite o incluso algún aditivo de limpieza actúa con más fuerza al ser nuevo aceite y desprende de las paredes partículas que estaban adheridas, el efecto de todo esto es que un aceite en condiciones iniciales al poco tiempo ya está contaminado inhabilitando su trabajo.
La ventaja de un sistema de riñón
Es más fácil y efectivo instalar un sistema de riñón en equipos críticos o volumen significativo de aceite, ya que el filtrado será automático, continuo, y no requiere mano de obra o planificación para filtrar.
Miramos lo que pasó con el conteo de partículas en esta máquina en forma grafica, mirando solamente las que son sobre 4 micrones por ml, después de instalar un sistema de filtración en riñón con un filtro de 4 𝜇m a beta 2000 (Donaldson P568666).
Notamos los resultados después de cinco horas de operación del equipo con el riñón instalado: El total de partículas sobre 4 𝜇m (línea azul) bajó de 147 mil por ml a 39 mil por ml (73% menos), y 5 horas más lo limpió a 9 mil partículas por ml (94% menos).
Al mismo tiempo, el nivel de partículas sobre 6 𝜇m (línea roja) que empezó con 35 mil por ml y había bajado a 700 por ml con la filtración y subido a 26 mil por ml mezclado, bajó a 8 mil, y después a casi 2 mil por ml.
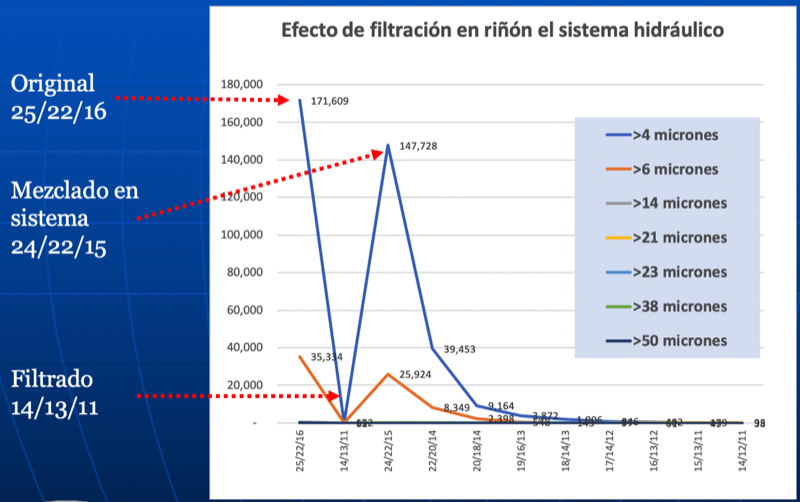
Todos sabemos que la vida útil del equipo depende de la condición del aceite, pero como vemos aquí, la idea de creer que solo tenemos que cambiar el aceite para hacer mantenimiento efectivo está equivocada. La lógica tradicional falla. No tenemos una manera de limpiar todo el sistema sin circular el aceite por ello, retirando continuamente hasta llegar al nivel optimo.
Lo interesante es que la instalación de un riñón no es difícil ni costosa. Solo requiere conectar una bomba al drenaje con un desvío, instalar un cabezal que reciba un filtro de alta eficiencia, y continuar las cañerías al reservorio para completar el circuito.
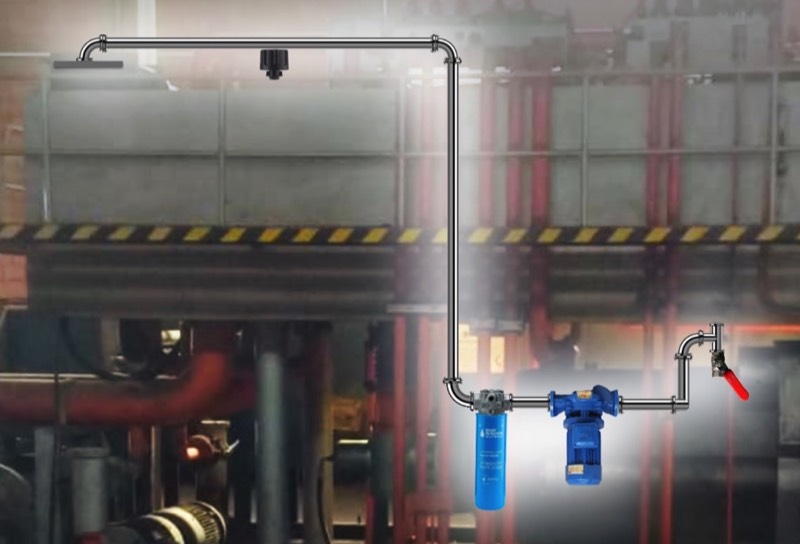
La información de este boletín técnico es de única y completa propiedad de Widman International S.R.L. Su reproducción solo será permitida a través de una solicitud a info@widman.biz no permitiendo que esta altere sus características ni su totalidad.
Visitantes a este sitio