
La implementación de buenas practicas en un mundo de gente conformista con procedimientos antiguos
Por Richard Widman
Muchas veces participamos de cursos, leemos libros, boletines, manuales de equipos, o viene un consultor con programas y recomendaciones que pueden reducir seriamente nuestros gastos de mantenimiento y mejorar la disponibilidad del equipo para mejorar la producción y utilidades de las plantas donde trabajamos, pero al implementarlos, encontramos obstáculos en la planta, sean con nuestros colegas, subordinados, jefes, o la misma gerencia y administración, donde prefieren quedarse en su zona de confort o simplemente tienen miedo al cambio y terminan haciendo lo que siempre hacían.
Este es el Boletín #193 de nuestro programa de Boletines Informativos mensuales. Todos los boletines están disponibles en formato pdf en https://www.widman.biz
El mes pasado escribimos en el boletín 192 sobre la manera de extender la vida útil de nuestro equipo hidráulico, utilizando análisis de aceite y filtros, y graficando los resultados, en una planta donde implementaron el riñón para filtración continuo. No pasó mucho tiempo en que un ingeniero de la planta sacó la bomba del riñón para un tanque hidráulico para utilizar en otro lado, sin entender el propósito del sistema de limpiar el fluido para un mejor funcionamiento.
La implementación de procedimientos requiere comunicación total. Cualquier cambio debe tener el respaldo del gerente, manager, jefe del área o CEO, aunque tal vez el no este totalmente convencido que tú idea sea buena. En este caso, los gráficos semana a semana, o mes a mes, serán las herramientas que muestren el resultado que se tiene en filtración, y haciendo otro gráfico similar de partículas de hierro y cobre, el gerente y los demás verán que el nivel de desgaste bajó.
Pero también requiere una comunicación dentro del equipo de mantenimiento, y a veces de producción. Conocemos casos donde instalan equipo de protección o riñón para filtración en plantas remotas donde la gente de producción tiene que prender el equipo, el riñón, o aumentar aceite, pero por no entender la importancia, mezclan aceites o no prenden el equipo de filtración o extracción de aire, causando fallas en el programa de mantenimiento y el equipo.
Los problemas de comunicación
Hay varias razones por la falta de entendimiento de la comunicación.
- A veces se instala algún equipo de protección, e instruye el operador o alguna persona de mantenimiento que se tiene que prenderlo, o cambiar cada “X” tiempo. Una explicación muy simple. Pero si la persona no entiende la razón, no sigue las instrucciones.
- Hay otros casos donde la explicación es tan complicada que no es entendida o lo que es peor, mal entendida. Años atrás, al editar un manual de mantenimiento, encontré el procedimiento de cambio de filtro del aire acondicionado de un edificio. Empezó explicando que se tenía que sacar el panel lateral del equipo para acceso, seguido por estos pasos:
- Seleccionar un destornillador #2 de estrella.
- Colocar el destornillador en la cabeza del tornillo localizado en la esquina inferior izquierda del lado derecha del equipo
- Girar el destornillador en el sentido contra el reloj hasta que salga completamente
- Colocar el tornillo en una lata.
- Proceder al tornillo inferior del medio del panel
- Colocar el destornillador en la cabeza de este tornillo
- Girar el destornillador en el sentido contra el reloj hasta que salga completamente
- Colocar el tornillo en una lata.
- Proceder al tornillo derecho del medio del panel
Uno de los problemas de este tipo de instrucción es que puede haber alguna instrucción crítica en el medio, como el cuidado de un bulbo de termostato, o la limpieza de este, que la gente no va a leer por aburrirse de las primeras líneas.
El otro problema es que la gente decide no leer lo demás del manual.
Cuando terminé de editar el manual completo, en lugar de un manual de 8 cm de grosor que nadie usaba quedó 2,2 cm de grosor, y se implementó fácilmente.
- Hay otros casos donde el personal que tiene que seguir los nuevos procedimientos y simplemente no cree que ayudará a bajar los costos o la carga de trabajo a lo largo. Personal que ha hecho lo mismo por 20 años, y no tiene ganas de cambiar. Incluido en eso esta la gente que nos pide aceite súper-obsoleto porque su manual del año 1950 lo recomienda. O por ejemplo que nos pide viscosidad monogrado SAE 40 para su motor de última generación.
- También hay casos donde hay conflictos de personal, o gente que se resiste a la idea de lo nuevo, ingenieros o mecánicos que entran sin considerar su educación, certificaciones, etc. En el boletín 51 identificamos las diferentes técnicas de trabajar con el personal, y la diferencia entre autoridad oficial y autoridad personal necesaria para la implementación.
Metas mal entendidas
Muchas veces el personal de operaciones o mantenimiento diario no entiende el objetivo del procedimiento. Pocos entienden la cantidad de tierra y contaminantes que entra por un respiradero de algún equipo y el daño que hará esa tierra cuando circule en el aceite. Y cuando se presentan los problemas, simplemente cambian aceite y vuelven a trabajar, sin corregir la causa.
Tampoco entienden que un cambio de aceite no siempre soluciona el problema, aunque instalen su filtro respiradero y revisen todos los retenes.
Aquí mostramos un ejemplo de un sistema hidráulico que lleva 5000 litros de aceite que estaba contaminado al 25/22/16 en la escala ISO 4406:99. Drenaron el aceite que podían (cerca de 4500 litros), limpiaron el tanque, filtraron ese aceite al 14/13/11 al colocarlo de nuevo. Después de operar la maquina 5 horas, la muestra de aceite tiene una limpieza ISO 4406:99 de 24/22/15. Los 500 litros que quedaron en los tubos y contaminantes pegados a diferentes superficies contaminaron el aceite filtrado, tal como hubiera contaminado aceite nuevo. Tal vez quedaron fibras o tierra de los trapos utilizados en la limpieza.
Aquí vemos las dos muestras, la muestra antes de la limpieza a la derecha, y la muestra del aceite limpio después de 5 horas de operación a la izquierda.
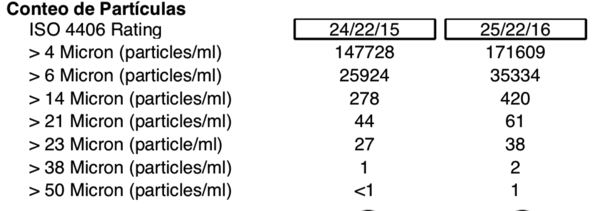
O sea, la solución no siempre es cambiar el aceite. Si el aceite es de buena calidad, y todavía tiene sus aditivos, sin ser contaminado por otro aceite, puede durar mucho más tiempo de lo que se acostumbra.
La cultura de excelencia
El desafío para muchos de nosotros no es implementar filtración, colocar filtros, filtrar aceite, engrasar con grasas correctas en la cantidad correcta, si no, conseguir que nuestra gente entienda que el éxito está en aprender a cuidar las cosas y buscar las mejores prácticas, participar en congresos de mantenimiento, charlar con sus colegas, asociarse con ingenieros de plantas similares para tener otras fuentes de información, etc.
A veces en lugar de dictar nuevos procedimientos, debemos preguntar a los trabajadores si conocen la razón detrás de sus procedimientos actuales, para recién explicar una manera mejor de hacerlo. Así sabemos el nivel de explicación que tendremos que utilizar, o el mito que tendremos que combatir. Hay gente que quiere detalle y necesita para entender, y gente que se aburre con detalle y solo quiere lo básico.
Muchas veces los ingenieros nos mencionan, por ejemplo, cuáles son los límites condenatorios en las pruebas de análisis, y si bien la literatura y experiencia de otros es importante, también lo es el hecho de formar una propia plataforma de análisis debido a que un mismo equipo o motor funcionará de diferente manera según el ambiente o condición en la que se encuentre (base fundamental del mantenimiento proactivo). Es así que es vital para el programa de mantenimiento crear esta cultura de excelencia. De principio no tiene que ser complicado como mostramos en el gráfico siguiente, luego uno debe crear el perfil propio para cada equipo encontrando nuevos objetivos e incluso sus propios límites condenatorios.
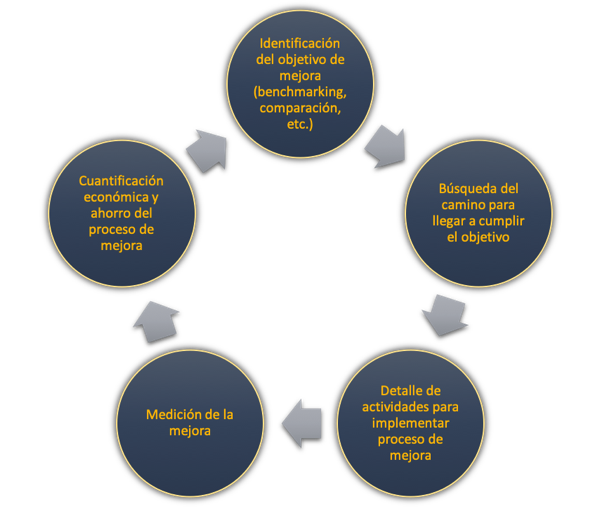
La clave de la implementación de lo que aprendemos es comunicación, y debemos buscar la manera de comunicar para que cada empleado entienda, no solo instruirlos y asumir que el mensaje fue entendido.
Como ejemplo, si dices a un entendido en mantenimiento de motores que haga cambiar el aceite del motor, automáticamente cambiará el filtro de aceite al mismo tiempo. Si das la misma instrucción a uno que no entiende, posiblemente no cambie el filtro porque no le has dicho que lo cambie.
Otro ejemplo es la alerta que implementaron en el tablero de muchos autos para indicar el momento correcto de cambiar el aceite. Es una luz que se prende cada “X” kilómetros, variado por las revoluciones del motor en ese periodo, la temperatura del aceite por tiempos, tramos de viajes, etc. (varia entre marcas). Pero no mide la calidad de aceite, ni su degradación. Es un calculador sofisticado. Sin embargo, cada semana alguien llega a la oficina o escribe en un foro que su aceite ya no sirve, aunque solo tenga 1000 km de recorrido, (o algo así) porque se prendió la luz. En realidad, el que hizo el último cambio se olvidó de resetear el contador que manda a prender la luz.
También hay gente que instruye y repite. Repetir lo mismo no hace entender a la persona que no ha entendido lo que quieres que haga. Solo le frustra, o aprende a no escuchar todo después de la primera vez, pensando que ya no hay nada nuevo.
Entonces hay que estar claro, sin aburrir. Muchas veces vale preguntar si entienden el propósito del nuevo procedimiento para poder aclarar dudas, pero nunca repetir como robot.
Hay que incentivar a los demás del equipo, no necesariamente con dinero, pero con reconocimientos, elogios, etc. Todos queremos hacer cosas que son elogiadas.
La información de este boletín técnico es de única y completa propiedad de Widman International S.R.L. Su reproducción solo será permitida a través de una solicitud a info@widman.biz no permitiendo que esta altere sus características ni su totalidad.
Visitantes a este sitio