
Tecnología en lubricación de reductores y cojinetes planos
Por Richard Widman
Durante el congreso internacional de Ingenieros de Mantenimiento en el mes de agosto en Santa Cruz - Bolivia, se podía observar muchos avances en tecnologías de materiales, técnicas de mantenimiento y productos de lubricación que pueden reducir el consumo de energía mientras aumentan la vida útil de las piezas. Nos parece interesante ver una de estas tecnologías.
Este es el Boletín #133 de nuestro programa de Boletines Informativos mensuales. Todos los boletines están disponibles en formato Acrobat pdf en http://www.widman.biz
Reductores
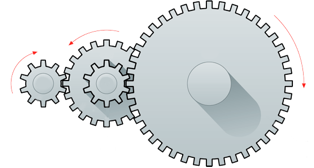
Por ejemplo cada vez que cambia de marcha en su automóvil, está utilizando engranajes de reducción para cambiar las revoluciones por minuto con el que opera el motor del vehículo. La reducción de engranajes no sólo proporciona diferentes velocidades de giro, dicha reducción también modifica la fuerza a la que éste puede girar.
Hay reductores en los autos, camiones, tractores, equipo de construcción, relojes, electrodomésticos, minas e industrias de todo tipo. Estos normalmente son utilizados para reducir la velocidad de un motor eléctrico o a combustible, o a veces hidráulico, a velocidades menores con una multiplicación de torque. A veces es solo para cambiar el ángulo de transmisión de la fuerza o para subir la velocidad con una reducción en el torque cuando se requiere alta velocidad pero no requiere tanta fuerza.
Para esta acción, se usa engranajes de diferentes tamaños y materiales. Si un engranaje es el doble de diámetro que el otro, gira a la mitad de la velocidad del primero, pero con el doble del torque. Se puede combinar varios engranajes en una caja reductora para aumentar más aun el torque o cambiar la velocidad. Otras veces se usa dos o tres reductores separados para poder lubricar cada uno de acuerdo a su fuerza y velocidad. Como explicamos en esta página con una calculadora de viscosidad, la viscosidad de aceite correcta para la lubricación depende principalmente de la velocidad final y la fuerza aplicada. O sea, si tenemos un motor de 5 hp y reducimos la velocidad a 2000 rpm en el reductor, necesitamos un aceite ISO 46, pero si ese motor es de 25 hp, requiere un aceite ISO 150. Y si reducimos la velocidad a 200 rpm, necesitamos un aceite ISO 320.
A veces la reducción es por un engranaje de bronce que gira contra un sinfín (como en la imagen). El lubricante debe ser uno que no daña el bronce por corrosión o daños físico/químico a la superficie del bronce.
El ángulo de los dientes de cada engranaje es diseñado para ser lo más eficiente y silencioso posible por la carga que lleva. Mayores ángulos generalmente requieren mayor protección EP.
Otras reducciones son hechas con correas o ruedas de goma que hacen tracción, o por poleas con cadenas como una bicicleta. La lubricación de estos se limita a sus bujes o, en el caso de cadenas, el interior de los eslabones, donde debemos buscar un lubricante que penetra y seca, dejando el interior lubricado con molibdeno u otro lubricante seco mientras el exterior queda seco para no atraer polvo o salpicar el ambiente con un lubricante liquido.
A medida que los engranajes se entrelazan unos con otros para realizar su función, aumentan las posibilidades de contacto entre las diversas superficies metálicas. Las superficies de los engranajes pueden presentar pequeñas irregularidades llamadas "asperezas". Cuando estas asperezas entran en contacto se produce una tremenda presión entre dichas partes, la cual puede causar diferentes tipos de desgaste capaces de acortar la vida de los engranajes mismos y provocar un aumento del tiempo perdido a causa de mantenimientos o reparaciones.
Los aceites para engranajes previenen estos problemas al formar una película de aceite entre las piezas que impide el contacto entre los metales. Los lubricantes para reductores contienen aditivos especiales que crean una capa protectora para proteger los dientes de los engranajes cuando la carga de trabajo a la que son sometidos es mayor que la que pueden soportar los aceites puros. Estas sustancias son conocidas como aditivos de extrema presión (EP).
El deterioro de los engranajes es por contacto entre los dientes, fatiga por temperaturas y molienda de partículas de tierra o desgaste, reacciones químicas, o corrosion. Es muy importante utilizar un aceite que tenga la viscosidad correcta, los mejores aditivos para los materiales usados, y un filtro en el respiradero que no solo elimina la tierra al respirar, sino también la humedad.
El eje de cada engranaje se apoya en un rodamiento o un cojinete plano. Estos requieren lubricante para separar las superficies y eliminar o reducir la fricción y/o desgaste. En un reductor de poca fuerza, como los engranajes de un reloj, se puede usar un aceite de muy baja viscosidad y un nivel muy bajo de aditivos (y solo una gota, ya que los puntos son tan pequeños que dos gotas chorrean, dejando el cojinete seco).
Los cojinetes de una planta industrial pueden ser grandes para apoyar engranajes de varios metros de diámetro, frecuentemente girando a 6 rpm o menos, con un torque enorme. Los Cojinetes siempre son fabricados de un material más blando que los ejes o soportes para concentrar el desgaste en una sola pieza reemplazable.
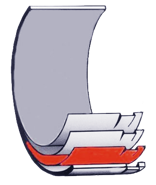
En motores y ciertas aplicaciones, estos son hechos de laminaciones de estaño y plomo sobre acero.
En la mayoría de los reductores que usan cojinetes, éstos son fabricados de bronce. Esto provee una superficie fuerte, pero más blando que los ejes. Bronce es una aleación (mezcla) de cobre y estaño.
Cuando un eje está girando a una velocidad alta, el modo de lubricación es hidrodinámico, o sea, no hay contacto entre el eje y el cojinete una vez que llega a su velocidad final, hasta el momento que se apaga y cae la velocidad. En este caso, el lubricante no requiere muchos aditivos EP, ya que hay poca operación en el modo de lubricación mixta o límite. Esta protección en lubricación límite puede ser suministrado por ZDDP o compuestos de Fósforo.
Cuando el eje opera a bajas revoluciones, la lubricación hidrodinámica está limitada a lo que su viscosidad puede soportar, causando un roce entre piezas cuando hay carga. Los aditivos protegen los dientes y los cojinetes cuando las presiones o pesos sobrepasan la carga que puede llevar esa viscosidad.
Tradicionalmente, la tecnología de Extrema Presión (EP) utilizado para proteger engranajes y los cojinetes que requieren este nivel de protección ha sido suministrada por un compuesto de Azufre y Fósforo. Este compuesto forma una capa gris a la superficie que se desliza y pela en condiciones de alta presión. Vuelve a formar su capa químicamente adherida hasta que se acaba su capacidad de reaccionar con el metal. La lubricación es mejor que aceite puro, pero en uso industrial su vida útil es limitada a unas 2500 horas o menos. Las temperaturas del reductor o cojinete suben gradualmente hasta un punto donde tiene que ser cambiado.
Además de una vida corta, este sistema de aditivos, cuando el engranaje o cojinete es de bronce, tiene la desventaja de llevar unos cuantos micrones de bronce cada vez que se pela. Este desgaste se ve en el análisis de aceite usado y el reparo del equipo antes de tiempo.
Tecnología
Desde unos 20 años atrás, poco a poco la ingeniería están descubriendo la tecnología de Borato Inorgánico. Aceites formulados con estos aditivos contienen millones de nano partículas de Borato. Estos actúan en forma polar (magnético). Esto quiere decir que pueden rodar en lugar de deslizar, reduciendo la temperatura. Además, al rodar o ser jalado del engranaje o cojinete, por no ser químicamente adherido, no pela nada de bronce.
En el siguiente cuadro podemos ver la diferencia en tamaño partículas de Borato, Grafito, y Molibdeno. Cada imagen representa un área de 2 micrones por 4 micrones.
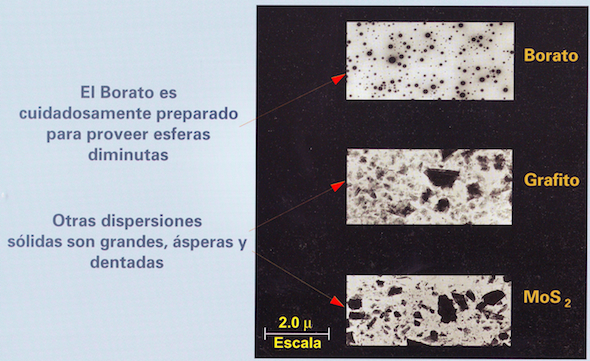
Desgaste reducido - Bronce
En una prueba de planta de un ingenio azucarero en temporada de zafra y producción, en cojinetes altamente cargados, enviamos dos aceites ISO 680 con aditivos de azufre/fósforo que fueron usados 2500 horas, al laboratorio para analizar el desgaste. El resultado mostró 800 ppm de desgaste de cobre (del bronce). Esto representa 320 ppm por cada mil horas de trabajo.
Se colocó un aceite ISO 680 con aditivos de Borato en estos cojinetes, y después de 5000 horas de trabajo, se envió las muestras al laboratorio, donde uno volvió con 4 ppm de cobre y el otro con 8 ppm. Esto representa 1,2 ppm por cada mil horas. Dejaron el aceite para la próxima zafra sin cambiar.
O sea, la reducción de desgaste fue de 320 ppm a 1,2 ppm por cada mil horas, y el aceite fue usado 10.000 horas en lugar de 2500. Claro que el aceite costó 20% más que el anterior, pero se utilizó 4 veces más tiempo con casi cero de desgaste. Un ahorro para la planta, y otro no menos importante para el medio ambiente.
Desgaste reducido - Hierro
En la misma planta, se analizó el aceite de un reductor grande que también usaba un aceite ISO 680 de una buena marca. El aceite tenía 2800 horas de uso y 700 ppm de hierro. Después de cambiar al Ultra Gear con Borato, usaron una zafra entera de 5000 horas. El laboratorio solo encontró 7 ppm de hierro. Decidieron correr una zafra más y después de 10.000 horas de uso solo tenía 15 ppm de hierro. Esto es una reducción de 280 ppm de desgaste de hierro por cada mil horas a 1,4 ppm por mil horas, además de una reducción de consumo de aceite de 75%. El impacto económico en esa empresa fue determinante para cambiar varias de sus políticas de mantenimiento.
Consumo de energía reducido
En otra prueba, una planta cambió los cinco litros de aceite azufre/fósforo ISO 320 para el de Borato en tres reductores. Antes del cambio registraron el amperaje y la temperatura de cada reductor. Al otro día, con las mismas condiciones, registraron estos valores de nuevo, como resultado obtuvieron un ahorro de 8,6% en el consumo de energía. Para los 7 reductores de la planta tuvieron un ahorro de $US 876 en la cuenta de electricidad, más la reducción en cantidad de aceite comprado y descartado. Esto ocurre debido a lo mencionado anteriormente que el borato al tener esas nano partículas, una parte ya está en la superficie del reductor y además esas “esferas pequeñas” ofrecen menor resistencia que el tradicional a reacción química.
En una prueba de planta de un ingenio azucarero en temporada de zafra y producción, en cojinetes altamente cargados, enviamos dos aceites ISO 680 con aditivos de azufre/fósforo que fueron usados 2500 horas, al laboratorio para analizar el desgaste. El resultado mostró 800 ppm de desgaste de cobre (del bronce). Esto representa 320 ppm por cada mil horas de trabajo.
Se colocó un aceite ISO 680 con aditivos de Borato en estos cojinetes, y después de 5000 horas de trabajo, se envió las muestras al laboratorio, donde uno volvió con 4 ppm de cobre y el otro con 8 ppm. Esto representa 1,2 ppm por cada mil horas. Dejaron el aceite para la próxima zafra sin cambiar.
O sea, la reducción de desgaste fue de 320 ppm a 1,2 ppm por cada mil horas, y el aceite fue usado 10.000 horas en lugar de 2500. Claro que el aceite costó 20% más que el anterior, pero se utilizó 4 veces más tiempo con casi cero de desgaste. Un ahorro para la planta, y otro no menos importante para el medio ambiente.
Desgaste reducido - Hierro
En la misma planta, se analizó el aceite de un reductor grande que también usaba un aceite ISO 680 de una buena marca. El aceite tenía 2800 horas de uso y 700 ppm de hierro. Después de cambiar al Ultra Gear con Borato, usaron una zafra entera de 5000 horas. El laboratorio solo encontró 7 ppm de hierro. Decidieron correr una zafra más y después de 10.000 horas de uso solo tenía 15 ppm de hierro. Esto es una reducción de 280 ppm de desgaste de hierro por cada mil horas a 1,4 ppm por mil horas, además de una reducción de consumo de aceite de 75%. El impacto económico en esa empresa fue determinante para cambiar varias de sus políticas de mantenimiento.
Consumo de energía reducido
En otra prueba, una planta cambió los cinco litros de aceite azufre/fósforo ISO 320 para el de Borato en tres reductores. Antes del cambio registraron el amperaje y la temperatura de cada reductor. Al otro día, con las mismas condiciones, registraron estos valores de nuevo, como resultado obtuvieron un ahorro de 8,6% en el consumo de energía. Para los 7 reductores de la planta tuvieron un ahorro de $US 876 en la cuenta de electricidad, más la reducción en cantidad de aceite comprado y descartado. Esto ocurre debido a lo mencionado anteriormente que el borato al tener esas nano partículas, una parte ya está en la superficie del reductor y además esas “esferas pequeñas” ofrecen menor resistencia que el tradicional a reacción química.
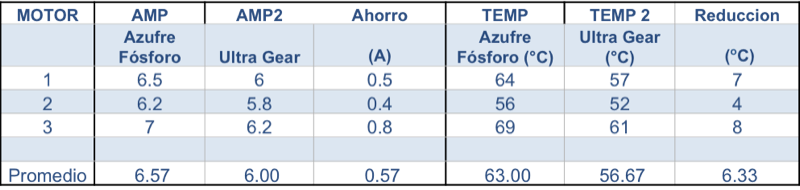
Resumen
Es claro que las tecnologías avanzan más rápido de lo que pensamos. Es fácil pensar que nuestro equipo tiene 40 años y por ende lo deberíamos continuar con las prácticas de mantenimiento que veníamos haciendo por todos estos años. A veces me dicen que esto debe ser para equipos de nuevas tecnologías, pero en este caso los equipos tenían más de 40 años de uso, aunque con muchas reparaciones, rellenados de engranajes, y cambios de cojinetes.
En la industria tenemos tantos avances como en autos. Solo que no tenemos un sistema de calificaciones como el API para separar los conceptos nuevos contra las viejas ideas o mitos. Tenemos que estudiar y consultar con los que sepan. Y debemos entender que una empresa que ofrece lubricantes que no tiene los aceites de última generación, no tienen interés en educar al usuario de sus beneficios.
También debemos reconocer que hay empresas que no tienen interés en vender un aceite que dura 4 veces más que los comunes cuando solo cuesta 20% más. Solo un proveedor que actúa como socio estratégico hará estas recomendaciones.
El problema es identificar los aceites de esta tecnología. Hay marcas que hablan maravillas de cualquier cosa. American Petroleum Co. usa el nombre “Supreme Ultra Gear”, pero otros usan el nombre Ultra Gear para productos de azufre/fósforo. Si la ficha técnica no indica Borato, seguro que no tiene.
Es claro que las tecnologías avanzan más rápido de lo que pensamos. Es fácil pensar que nuestro equipo tiene 40 años y por ende lo deberíamos continuar con las prácticas de mantenimiento que veníamos haciendo por todos estos años. A veces me dicen que esto debe ser para equipos de nuevas tecnologías, pero en este caso los equipos tenían más de 40 años de uso, aunque con muchas reparaciones, rellenados de engranajes, y cambios de cojinetes.
En la industria tenemos tantos avances como en autos. Solo que no tenemos un sistema de calificaciones como el API para separar los conceptos nuevos contra las viejas ideas o mitos. Tenemos que estudiar y consultar con los que sepan. Y debemos entender que una empresa que ofrece lubricantes que no tiene los aceites de última generación, no tienen interés en educar al usuario de sus beneficios.
También debemos reconocer que hay empresas que no tienen interés en vender un aceite que dura 4 veces más que los comunes cuando solo cuesta 20% más. Solo un proveedor que actúa como socio estratégico hará estas recomendaciones.
El problema es identificar los aceites de esta tecnología. Hay marcas que hablan maravillas de cualquier cosa. American Petroleum Co. usa el nombre “Supreme Ultra Gear”, pero otros usan el nombre Ultra Gear para productos de azufre/fósforo. Si la ficha técnica no indica Borato, seguro que no tiene.
Widman International SRL contribuye a la capacitación de los ingenieros y usuarios para mejorar su competitividad. Para mayores informaciones prácticas, visite nuestra página Web: www.widman.biz
La información de este boletín técnico es de única y completa propiedad de Widman International S.R.L. Su reproducción solo será permitida a través de una solicitud a info@widman.biz no permitiendo que esta altere sus características ni su totalidad.
La información de este boletín técnico es de única y completa propiedad de Widman International S.R.L. Su reproducción solo será permitida a través de una solicitud a info@widman.biz no permitiendo que esta altere sus características ni su totalidad.
Visitantes a este sitio
12,782,466